The Importance of Packaging Machine Repair for Business Continuity
The Importance of Packaging Machine Repair for Business Continuity
Blog Article
The Ultimate Guide to Packaging Device Repair: Maintain Your Procedures Running Smoothly
Comprehending the complexities of product packaging device repair is important for keeping ideal performance and lessening disturbances. Routine maintenance not just expands the life of these makers however likewise addresses common problems that can impede performance.
Importance of Normal Upkeep
Regular maintenance of product packaging makers is vital for ensuring optimal efficiency and long life. By implementing a structured maintenance routine, drivers can determine prospective concerns prior to they escalate into substantial issues. This aggressive technique not only minimizes downtime but likewise extends the lifespan of the equipment, ultimately bring about minimized operational expenses.
Regular inspections permit for the assessment of crucial parts such as belts, seals, and sensors. Dealing with damage immediately prevents unanticipated failings that might interrupt manufacturing and cause costly fixings. Furthermore, regular maintenance aids guarantee conformity with market standards and regulations, cultivating a risk-free working atmosphere.
Moreover, maintenance tasks such as lubrication, cleansing, and calibration dramatically boost device efficiency. Enhanced efficiency converts to regular item quality, which is essential for keeping consumer fulfillment and brand name online reputation. A well-maintained product packaging maker runs at ideal speeds and decreases material waste, adding to general efficiency.
Typical Packaging Device Concerns
Packaging devices, like any complex equipment, can run into a selection of typical problems that might impede their efficiency and effectiveness - packaging machine repair. One prevalent issue is irregular sealing, which can cause product wasting and wastage if packages are not correctly secured. This typically results from misaligned components or used sealing elements
An additional regular concern is mechanical jams, which can take place because of international objects, worn components, or improper placement. Jams can cause hold-ups in manufacturing and rise downtime, inevitably affecting total efficiency. Furthermore, digital breakdowns, such as failure in sensing units or control systems, can lead and interrupt operations to imprecise measurements or irregular device actions.
Moreover, issues with item feed can likewise emerge, where things might not be delivered to the packaging area regularly, causing disturbances. Wear and tear on rollers and belts can lead to suboptimal performance, needing prompt attention to stop more damage.
Understanding these typical concerns is vital for preserving the stability of packaging operations, making certain that machinery runs smoothly and efficiently, which subsequently aids in conference production targets and preserving item top quality.

Fixing Methods
Effective repairing methods are important for promptly resolving problems that arise with product packaging devices. A systematic strategy is important for identifying the source of breakdowns and reducing downtime. Begin by collecting info concerning the signs observed; this might include uncommon noises, functional delays, or error codes shown on the machine's user site web interface.
Next, describe the machine's handbook for troubleshooting guidelines details to the design in question. This source can offer valuable understandings into typical problems and suggested diagnostic steps. Utilize visual inspections to look for loose connections, used belts, or misaligned elements, as these physical variables commonly add to functional failings.
Execute a procedure of removal by screening specific device features. If a seal is not developing appropriately, analyze the sealing mechanism and temperature level settings to figure out if they fulfill functional requirements. Document each step taken and the results observed, as this can help in future repairing efforts.
Repair work vs. Substitute Choices
When faced with equipment malfunctions, choosing whether to repair or replace a packaging maker can be a complicated and important selection. This decision rests on several key variables, consisting of the age of the device, the degree of the damages, and the predicted influence on operational performance.
To start with, take into consideration the device's age. Older equipments might need even more constant repair work, leading to greater cumulative expenses that can go beyond the investment in a brand-new unit. In addition, review the severity of the malfunction. Small problems can usually be solved quickly and economically, whereas considerable damages might demand a substantial monetary commitment for repair services.
Operational downtime is another important consideration. Investing in a new machine that offers improved effectiveness and integrity might be extra prudent if repairing the equipment will certainly trigger long term hold-ups. Take into consideration the availability of components; if replacement components are difficult to come by, it might be extra critical to change the equipment totally.
Inevitably, performing a cost-benefit evaluation that includes both long-term and immediate effects will help in making an educated choice that aligns with your monetary restraints and functional objectives. (packaging machine repair)
Preventive Steps for Long Life
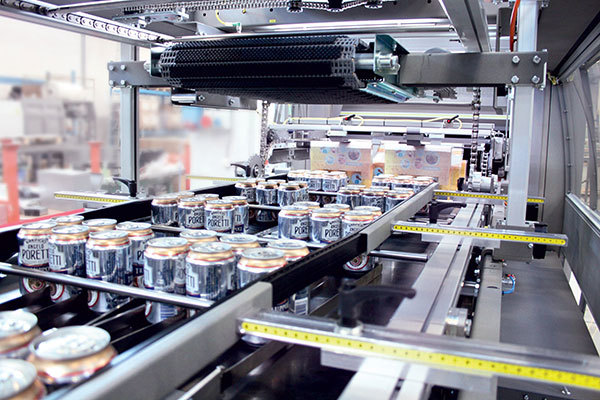
Secret safety nets include routine lubrication of moving parts, positioning checks, and calibration of controls navigate here and sensing units. Establishing a cleaning schedule to get rid of debris and pollutants from machinery can considerably minimize damage (packaging machine repair). Furthermore, checking operational parameters such as temperature and resonance can aid discover abnormalities beforehand
Training personnel to identify signs of wear click here for more info or breakdown is an additional important component of preventive maintenance. Empowering operators with the expertise to do standard troubleshooting can lead to quicker resolutions and reduce functional disturbances.
Documentation of maintenance activities, consisting of solution records and assessment findings, cultivates responsibility and facilitates educated decision-making relating to fixings and replacements. By focusing on preventive steps, companies can guarantee their packaging devices operate at peak performance, inevitably causing boosted performance and lowered operational prices.
Conclusion
In conclusion, the reliable maintenance and repair of product packaging equipments are paramount for sustaining functional efficiency. By implementing preventative procedures, companies can improve device longevity and make sure undisturbed performance in packaging procedures.
Recognizing the complexities of product packaging device repair work is essential for preserving optimal efficiency and decreasing interruptions.Regular maintenance of packaging devices is essential for ensuring ideal performance and durability.Packaging equipments, like any kind of intricate machinery, can run into a variety of typical problems that might impede their performance and effectiveness. If repairing the equipment will cause prolonged hold-ups, investing in a brand-new machine that offers enhanced effectiveness and integrity might be a lot more prudent.In verdict, the efficient maintenance and repair work of packaging equipments are paramount for sustaining operational effectiveness.
Report this page